Battery & Device Repair
Repairs of a special nature are a constant companion in the industrial use of aggregates and especially electromechanical tools. Regardless of which products one speaks of, tools and devices (electropneumatic and hydraulic), clamping devices, electronic or battery-powered drives, battery chargers, electronic control units, and also rechargeable batteries are subjected to constant use in work shifts.
This means, in the most extreme cases, 20-24 hours of continuous operation, naturally leading to wear and tear, up to malfunction and subsequent failure. These technical applications are found not only in pure production plants but also in other industrial sectors.
When there's no room
for error
When it comes to the use of tools, equipment, and electronic components, there's a classic target audience for highly demanding applications. These include, among others, the repair of ships or logistics companies at the port, steel and thermal power plants, service companies, and production facilities for wind energy or rotor blades, in public organizations such as the THW, the fire department, or the Bundeswehr.
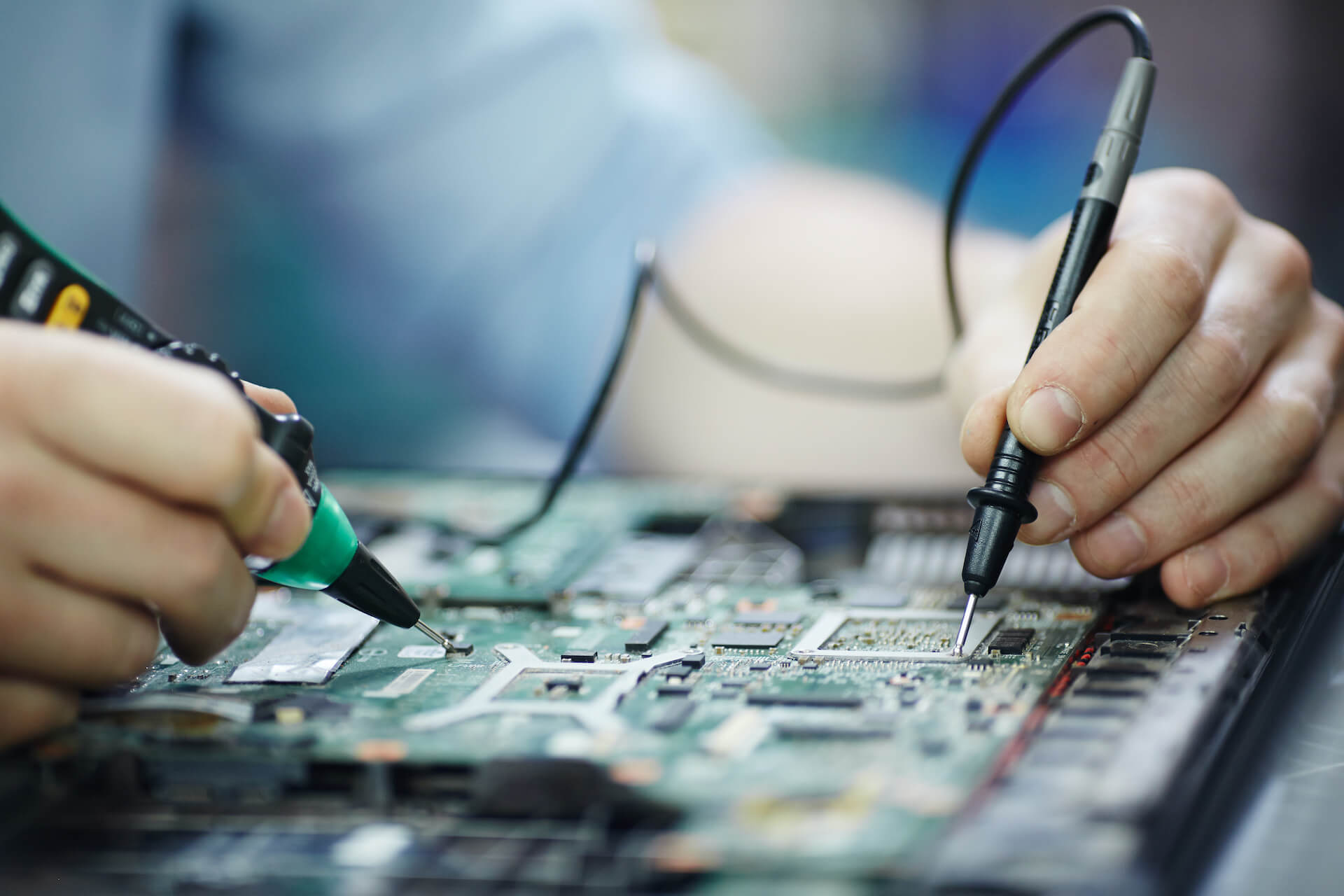
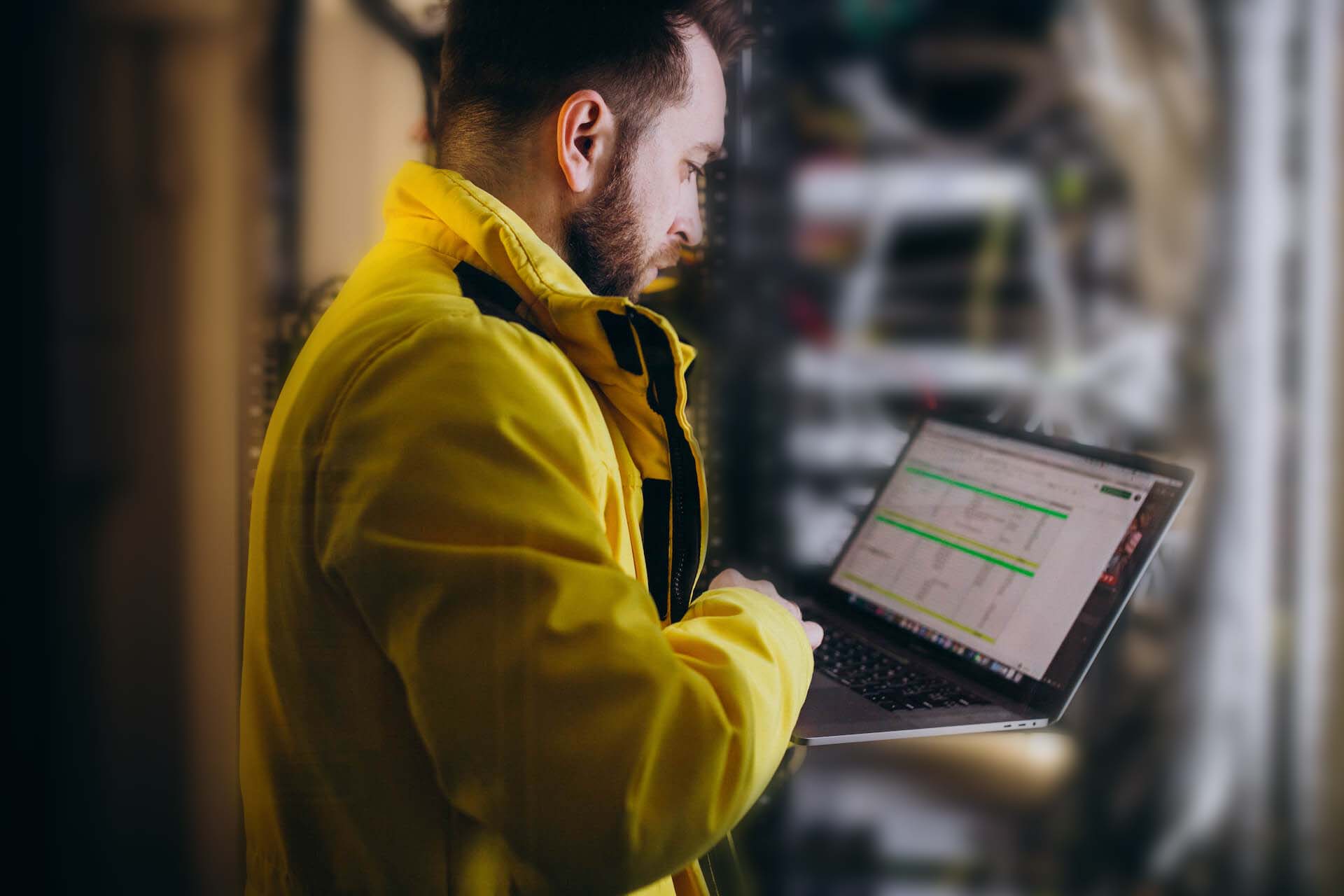
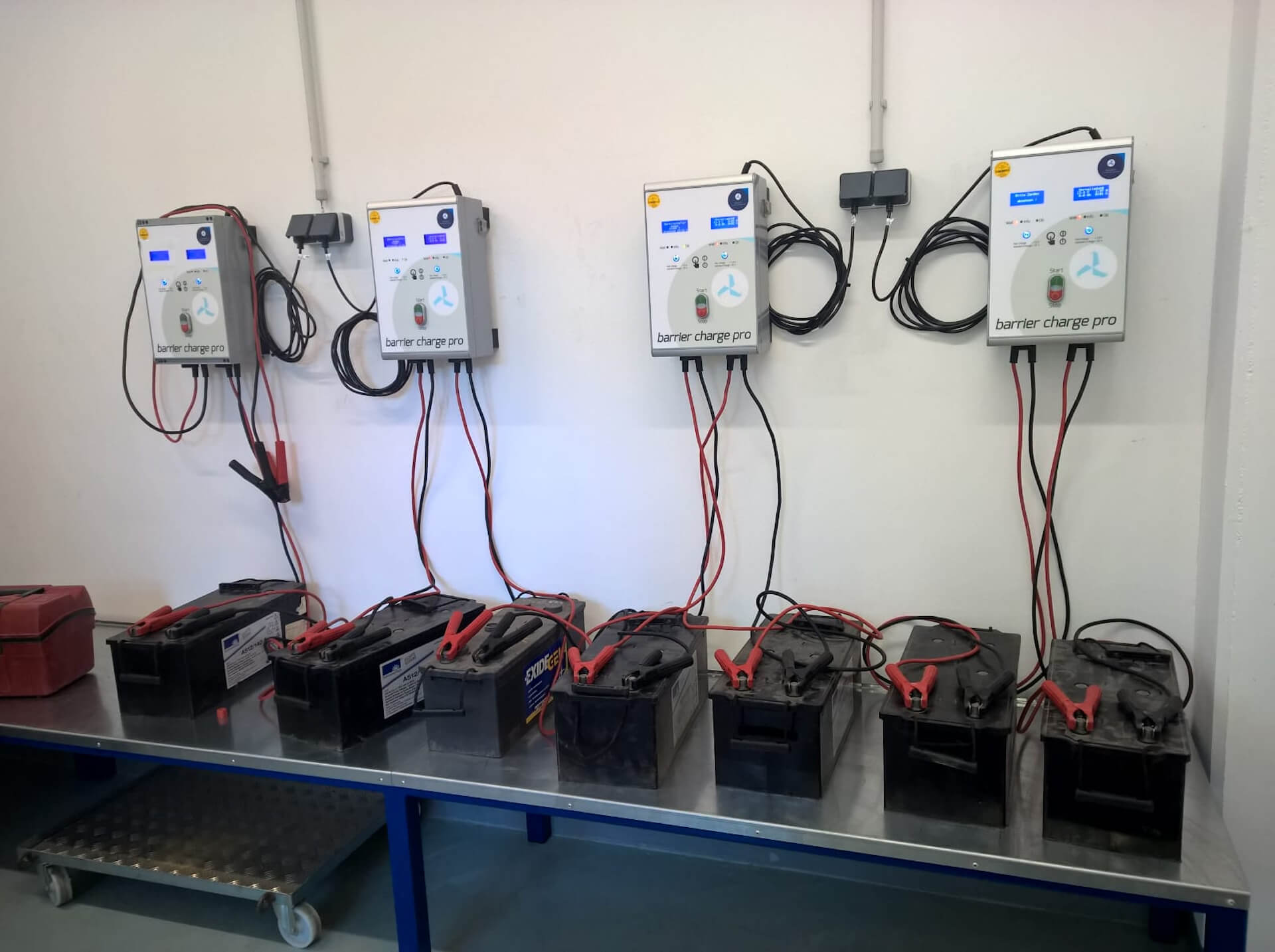
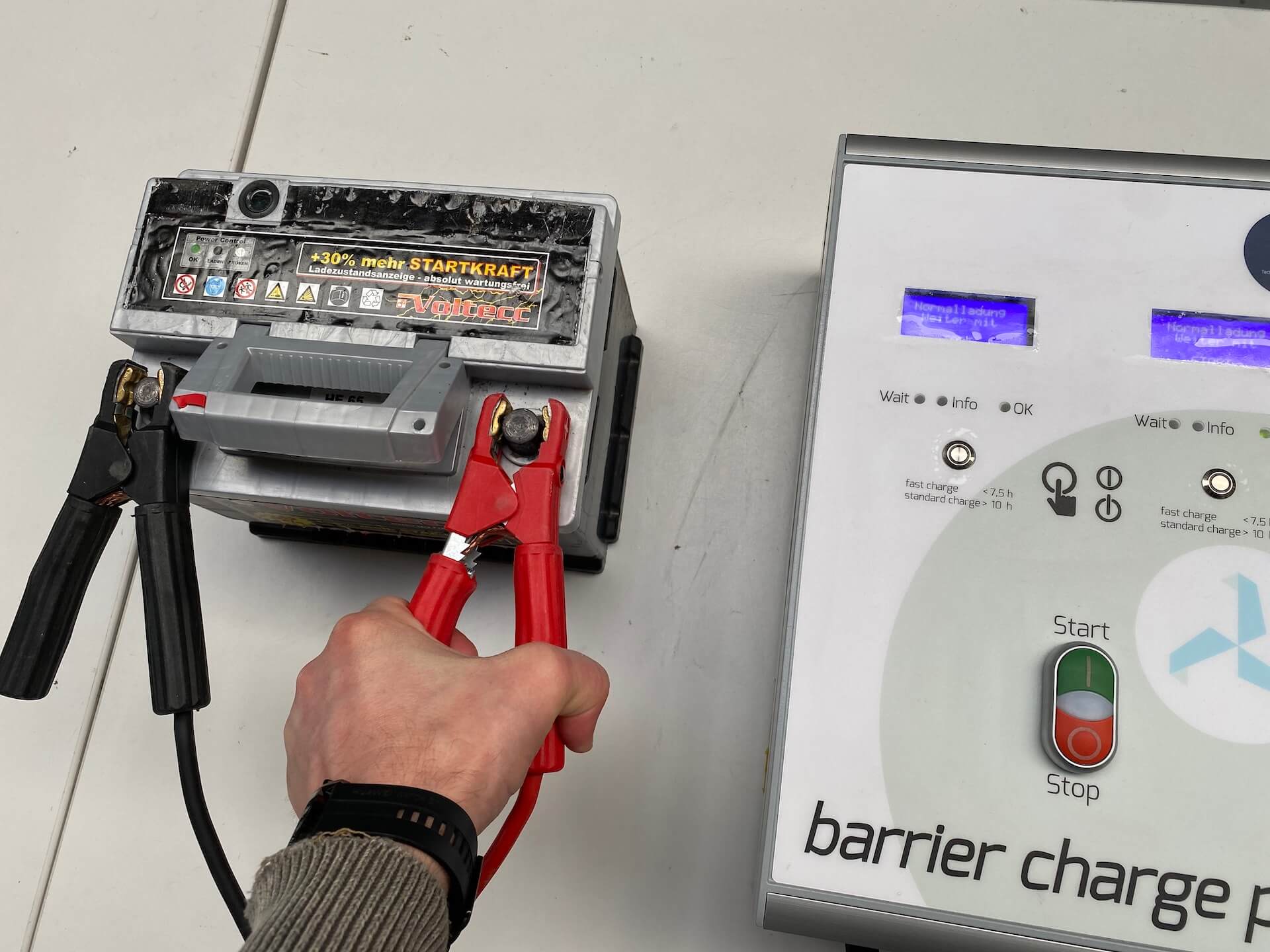
Tool repairs
in various fields
The second group of businesses combines aging and heat- or weather-exposed applications, such as electronic devices and drives. This typically includes service and assembly companies that we support with our repair service for electronic components.
These can be: Logistics companies or manufacturers of material handling equipment like forklifts or Automated Guided Vehicles (AGVs), manufacturers of rehabilitation devices such as wheelchairs or motor-assisted aids for medical transport, producers facing challenges in reworking electronic components after the end of series production. Customers needing repair of charging electronics and chargers, e.g., for generously equipped mobile homes, boats, or devices used for charging batteries in electric vehicles (wallbox, EV charger, e-mobility).
Up to battery control and, if necessary, the repair of modern vehicle batteries themselves.
If repair departments exist within the companies, it is essential to work efficiently to maintain profitability. This means restoring availability for the failed module, battery charger, or battery-powered tool within a relatively short time frame to avoid the need for replacement procurement.
While this is theoretically understandable, in everyday practice, the availability of spare parts is often a problem. Repair itself is often only a part of the important work. It is necessary to clearly identify the object to be repaired based on the label on the casing, which is often barely possible due to intensive use. Then, the components need to be researched from the available exploded drawings, if they exist, as sometimes model changes have already been made by the manufacturer due to the age. Finally, it is necessary to find the suitable, ideally local supplier. This supplier is contacted, and the written information is transmitted multiple times to later make a comparison of suppliers and ultimately also a comparison of purchase prices in terms of profitability.
The determined time share of administrative work, which really has nothing to do with the actual repair, averages about 60-70% of the total repair effort! Once a structure for the maintenance processes of a repair part has been established, significantly less is required from the second run onwards, but still regularly around 25-30% of the total repair time. Significant time savings are possible with the Nordisch E-Teile Service.
Devices, hand tools, electronics change within increasingly shorter periods. The so-called "product life cycle" has been reduced from 6 to about 2.5 years in many technical applications. At international technology exhibitions such as "MOTEK," new or modified technical products are presented every 2 years, exclusively intended for professional or industrial users.
Instead of cable-guided power tools, there are battery-operated tools. Instead of gauges or dial indicators, there are intelligent components that enable data transmission of information from the control unit of the device, the battery, or the tool directly via radio and thus secure seamless documentation of processes.
This development continues in technical B2B sectors. Our economy demands constant technological advancement to remain and permanently attractive as a production location.
On the other hand, it is a logistical and administrative challenge to have many different products, devices, or components with a high number of different technological levels in use. You need your own drawings, article numbers, parts, possibly special tools, availability, and suitable suppliers for each variant! This is where you should specialize, like the repair department at Nordisch.
In the example of the automotive industry, e.g., at Volkswagen, BMW, Daimler, AUDI, and many other manufacturers worldwide, there are often the most diverse work processes in one factory, from body construction to painting and final assembly. In the supplier industry, electrical industry, aviation industry, and public enterprises, there are rather pure assembly tools, electronic test equipment, and battery chargers in use and thus regularly repaired.
For general industry, repairs are more likely to be found in hand tools and hydraulic systems. The level of complexity in the industrial maintenance of tools and equipment varies greatly among the aforementioned customer groups. Therefore, a very high level of expertise and practical qualification is necessary in processing these repair cases.
Summary of Critical Factors that Can Lead to Problems
for Repairs in Large Enterprises during Maintenance:
- Do I have the routine? (My strength lies in the core tasks of our company).
- Is additional time required? (Malfunctions in the component/device lead to additional work).
- What do I do in case of staff shortage? (Repairs require additional staff, e.g., during illness or vacation).
- Can I guarantee quick availability? (Long waiting times mean increased demand for devices/spare parts as a contingency).
Possible Outcome:
Ineffective (1.) Uncertainty + (2.) Time Pressure + (3.) Additional Staffing Requirements + (4.) Spare Part Costs
Conclusion:
A repair in your own company should definitely be evaluated based on the following criteria. If the final evaluation is still favorable, the repair operation can be carried out without economic disadvantage.
Options for Coping with Repair and Spare Part Problems - Measures of Assistance
If a repair is to be carried out in your own company with a maintenance department, it is advisable to optimize the pure repair time and keep administrative tasks out of the technical employee's work process. This means: Use of web-based tools to facilitate selection and supply, e.g., by means of digitized exploded drawings. - Accompanied by a specialized supplier who can deliver brand-independent spare parts and possibly keep them available.
Your tools and components will be digitized free of charge within a short time and activated for the online spare parts database. A spare parts list for all repair orders is automatically compiled within minutes and can be forwarded, for example, by email.
The work effort is max. only 2-3 minutes per repair order!
To avoid unnecessarily increasing the costs for emergency supplies of electronic components and tools, especially for medical technology repairs and special battery repairs, it is advisable to minimize the throughput time.
This means:
- Choose a regional service partner who works independently of brands and whose shipping time does not exceed your maximum desired transport time. A shipping time of up to 3 days is common, anything more is too much.
- Make use of organized shipping services such as pick-up service and shipping service with logistics box by the repair service provider.
- Check the accessibility of your contact person for repairs, e.g., for multi-shift operations after 6:00 p.m.
Repair Service
We ensure accessibility around the clock with our intake form. Whether it's planned pickup/shipping or just information about repair measures you're after, we've got you covered. Upon receipt of your repair parts, all processes are initiated, and you'll receive your free estimate within max. 5 business days.
If a repair seems uneconomical, we're happy to offer you a replacement if needed.
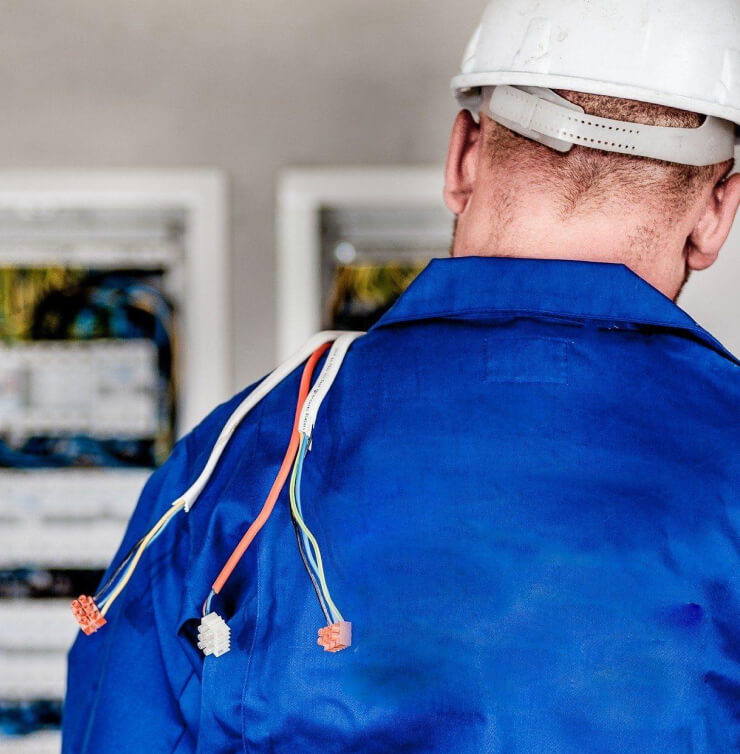