Nordisch GmbH
Professional Battery and Charging Technology
for Demanding Applications!
Your Nordisch team stands for application-oriented technology and a service-focused approach to everything related to batteries. From product trading, development, and design to repairing both simple and complex technologies—our customers in industry and the SME sector benefit from long-term relationships and the experience gained from them.
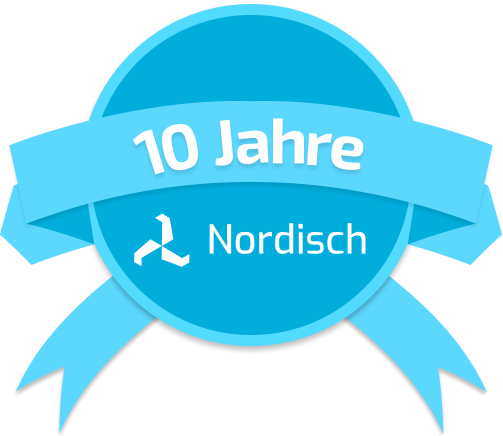
Who We Are...
Below you will find a brief description of us and the work that the Nordisch team carries out for you.
Head of Technical Development, Sales, and Service
The owner Marcus Runge initially trained in mechanical engineering and later graduated as an industrial engineer specializing in production economics and capital goods marketing. He gained professional experience in major, renowned German industrial companies. For over 20 years, he has held managerial positions, always working as a "problem solver" for the economic implementation of processes in the assembly industry. For more than 10 years now, he has been running his own company specializing in battery and charging technology. Through innovative developments and application-oriented solutions in the field of electromechanical equipment, he has been able to expand his numerous industry contacts, with Nordisch customers now found worldwide.
Administration/Internal Services
Questions about invoices, quotes, or delivery status? The internal service is staffed by up to 2 employees at all times. This ensures availability for our customers during office hours. If we are occasionally unavailable outside office hours or if the phone line is busy, our voicemail and various contact options on the website are available to you as alternatives.
Service
Repairs, cost estimates, or technical questions: Our service team is also permanently staffed by up to 2 employees. Here, technical devices and batteries of any technology, UPS systems, power supplies, or battery charging cables are brought back to life, even in "difficult cases"! Every delivered item is registered at goods receipt, assessed, spare parts are identified, and a cost estimate is prepared. If an on-site appointment is required, this can also be arranged nationwide. With extensive global supplier contacts, the Nordisch spare parts service can help you obtain hard-to-find electronic components. Services include not only repairs and battery damage analysis but also the special procurement and needs-based supply of discontinued and hard-to-find electronic components or the production of custom batteries.
Production
The final assembly of designed assemblies is order-dependent. Up to 6 of our own employees, as well as several external subcontractors, suppliers, designers, and software developers, are engaged in producing the required products. Materials stored for our customers are picked here and processed in sequence according to a "routing card." The designated materials are processed into modular assemblies and assembled into the final product. Software and firmware are approved, and a final functional test ensures the promised properties and functions before delivery. After successful quality control, the goods are then dispatched.